La fibre de carbone, composée de matériaux différents (fibre et résine), sa variabilité et, par conséquent, sa personnalisation sont au cœur de son attrait. En remplacement du métal, les composites en fibre de carbone offrent une résistance dix fois supérieure à celle de l'acier. Les fabricants de fibre de carbone créent des produits similaires, mais non identiques. La fibre de carbone varie en termes de module de traction (ou rigidité déterminée par la déformation sous contrainte) et de résistance à la traction, à la compression et à la fatigue.
La fibre de carbone à base de PAN est aujourd'hui disponible en faible module (moins de trente-deux millions de lbf/in² ou Msi), module standard (33 à trente-six Msi), module intermédiaire (40 à cinquante Msi), module élevé (50 à soixante-dix Msi) et module ultra élevé (70 à cent quarante Msi).
En termes simples, la fibre de carbone est créée par la transformation d'un précurseur de fibre organique en atmosphère inerte à des températures supérieures à 982,22 °C (1 800 °F). La fabrication de fibre de carbone peut toutefois être une activité complexe.
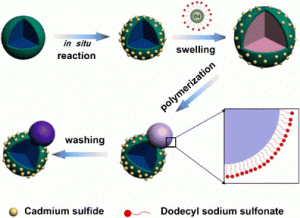
Polymérisation et filage
Polymérisation
Le processus commence par un composé chimique, appelé précurseur, qui constitue la structure moléculaire de la fibre. Aujourd'hui, près de 100 % de la fibre de carbone produite est constituée de précurseurs à base de tissu ou de brai, mais la majeure partie provient du polyacrylonitrile (PAN), fabriqué à partir de nitrite, lequel provient de produits chimiques industriels tels que le propane et l'ammoniac.
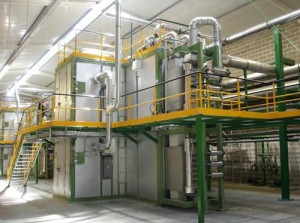
Oxydation et carbonisation
Oxydation
Ces bobines sont chargées dans le panier et, lors de la phase d'oxydation, la plus longue de la production, les fibres de PAN passent par une série de fours dédiés. Avant d'entrer dans l'appareil de cuisson principal, les fibres de PAN sont transformées en une étoupe ou une feuille appelée chaîne. La température de la chambre varie entre environ 200 °C et 300 °C.
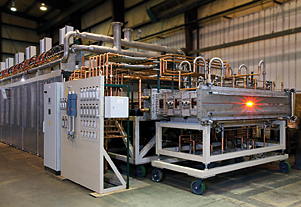
Traitement de surface et dimensionnement
Traitement de surface et dimensionnement
L'étape suivante est essentielle à la performance des fibres et, outre les précurseurs, elle permet de distinguer au mieux le produit d'un fournisseur de celui de ses concurrents. L'adhérence entre le composé organique de la matrice et les fibres de carbone est essentielle au renforcement du composite ; tout au long du processus de production des fibres de carbone, un traitement de surface est effectué pour renforcer cette adhérence.
Date de publication : 01/11/2018