فیبر کربن، که از ترکیب مواد متفاوت (فیبر و رزین) تشکیل شده است، تنوع آنها و بنابراین، قابلیت سفارشیسازی، از جذابیت اصلی آنهاست. کامپوزیتهای فیبر کربن به عنوان جایگزین فلز، ده برابر فولاد استحکام دارند. تولیدکنندگان فیبر کربن محصولاتی تولید میکنند که مشابه اما نه یکسان هستند. فیبر کربن از نظر مدول کششی (یا سختی که به عنوان تغییر شکل زیر کرنش تعیین میشود) و استحکام کششی، فشاری و خستگی متفاوت است.
الیاف کربن مبتنی بر PAN امروزه در مدول پایین (کمتر از سی و دو میلیون پوند-نیرو در اینچ مربع یا Msi)، مدول معمولی (۳۳ تا سی و شش Msi)، مدول متوسط (۴۰ تا پنجاه Msi)، مدول بالا (۵۰ تا هفتاد Msi) و مدول فوق العاده بالا (۷۰ تا صد و چهل Msi) موجود است.
به عبارت ساده، الیاف کربن با انتقال الیاف پیشساز آلی در اتمسفر خنثی در دمای بالاتر از ۱۸۰۰ درجه فارنهایت (۹۸۲.۲۲ درجه سانتیگراد) تولید میشوند. با این حال، تولید الیاف کربن میتواند یک فرآیند پیشرفته باشد.
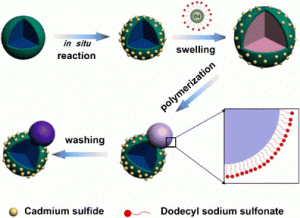
پلیمریزاسیون و ریسندگی
پلیمریزاسیون
این فرآیند با یک ماده اولیه شیمیایی به نام پیشساز آغاز میشود که ستون فقرات مولکولی فیبر را تشکیل میدهد. امروزه، تقریباً ۱۰۰ درصد فیبر کربن تولید شده از پارچه یا پیشسازهای مبتنی بر قیر ساخته میشود، اما بیشتر آن از پلیآکریلونیتریل (PAN) که از نیتریت تولید میشود، به دست میآید و نیتریت از مواد شیمیایی صنعتی پروپان و آمونیاک به دست میآید.
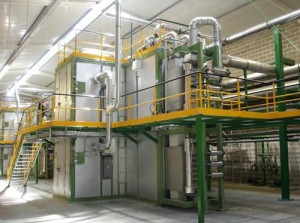
اکسیداسیون و کربنیزاسیون
اکسیداسیون
این بوبینها درون سبد قرار میگیرند و در طولانیترین مرحله تولید، یعنی مرحله اکسیداسیون، الیاف PAN از طریق یک سری کورههای اختصاصی تغذیه میشوند. قبل از ورود به دستگاه اصلی آشپزخانه، الیاف PAN به صورت یک طناب یا ورق به نام تار در میآیند. دمای محفظه از 392 درجه فارنهایت (حدود 200 درجه سانتیگراد) تا 572 درجه فارنهایت (300 درجه سانتیگراد) متغیر است.
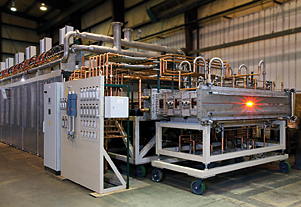
عملیات سطحی و اندازه گذاری
عملیات سطحی و اندازه گذاری
مرحله بعدی برای عملکرد الیاف ضروری است و علاوه بر پیشسازها، به بهترین شکل محصول یک تأمینکننده را از محصول رقبا متمایز میکند. چسبندگی بین ترکیب آلی ماتریس و الیاف کربن برای تقویت کامپوزیت ضروری است؛ در طول فرآیند تولید الیاف کربن، یک عملیات سطحی برای افزایش این چسبندگی انجام میشود.
زمان ارسال: نوامبر-01-2018