คาร์บอนไฟเบอร์ประกอบด้วยวัสดุต่างชนิดกัน (ไฟเบอร์และเรซิน) โดยความหลากหลายและความสามารถปรับแต่งได้นั้นถือเป็นหัวใจสำคัญของความสวยงามของคาร์บอนไฟเบอร์ คาร์บอนไฟเบอร์เป็นวัสดุทดแทนโลหะที่มีความแข็งแรงมากกว่าเหล็กถึง 10 เท่า ผู้ผลิตคาร์บอนไฟเบอร์ผลิตผลิตภัณฑ์ที่คล้ายคลึงกันแต่ไม่เหมือนกัน คาร์บอนไฟเบอร์มีค่าโมดูลัสแรงดึง (หรือความแข็งที่กำหนดโดยการเสียรูปภายใต้แรงเครียด) และความแข็งแรงแรงดึง แรงอัด และความล้าที่แตกต่างกัน
ปัจจุบันเส้นใยคาร์บอนที่ใช้ PAN สามารถหาได้ในระดับโมดูลัสต่ำ (น้อยกว่า 32 ล้าน lbf/in² หรือ Msi) โมดูลัสมาตรฐาน (33 ถึง 36 Msi) โมดูลัสระดับกลาง (40 ถึง 50 Msi) โมดูลัสสูง (50 ถึง 70 Msi) และโมดูลัสสูงมาก (70 ถึง 140 Msi)
หากอธิบายอย่างง่ายที่สุด คาร์บอนไฟเบอร์ถูกสร้างขึ้นโดยการย้ายเส้นใยสารตั้งต้นอินทรีย์ในบรรยากาศเฉื่อยที่อุณหภูมิสูงกว่า 1,800°F (982.22 °C) อย่างไรก็ตาม การผลิตคาร์บอนไฟเบอร์อาจเป็นธุรกิจขั้นสูง
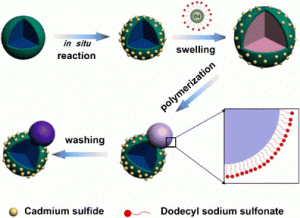
การเกิดพอลิเมอไรเซชันและการปั่น
การเกิดพอลิเมอไรเซชัน
กระบวนการเริ่มต้นด้วยสารประกอบเคมีที่เป็นวัตถุดิบหลักซึ่งเรียกว่าสารตั้งต้นที่มีโครงสร้างโมเลกุลของเส้นใย ปัจจุบัน เส้นใยคาร์บอนที่สร้างขึ้นประมาณ 100 เปอร์เซ็นต์นั้นทำจากผ้าหรือสารตั้งต้นที่ทำจากน้ำมันดิน อย่างไรก็ตาม ส่วนใหญ่มาจากโพลีอะคริโลไนไตรล์ (PAN) ซึ่งผลิตจากไนไตรต์ และไนไตรต์มาจากโพรเพนและแอมโมเนีย ซึ่งเป็นสารเคมีในอุตสาหกรรม
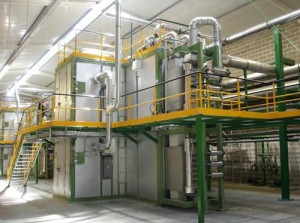
ออกซิเดชันและคาร์บอนไนเซชัน
ออกซิเดชัน
เมื่อบรรจุแกนม้วนเส้นใยลงในตะกร้าและภายในระยะออกซิไดซ์ของการผลิตที่ยาวนานที่สุด เส้นใย PAN จะถูกป้อนผ่านเตาเผาเฉพาะชุดหนึ่ง ก่อนที่จะเข้าสู่เครื่องใช้ในครัวหลัก เส้นใย PAN จะถูกห่อหุ้มเป็นเส้นใยหรือแผ่นที่เรียกว่าเส้นยืน อุณหภูมิของห้องจะอยู่ระหว่าง 392 °F (ประมาณ 200 °C) ถึง 572 °F (300 องศาเซลเซียส)
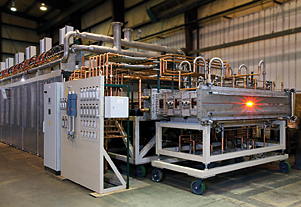
การปรับปรุงพื้นผิวและการกำหนดขนาด
การปรับปรุงพื้นผิวและการกำหนดขนาด
ขั้นตอนต่อไปมีความสำคัญต่อประสิทธิภาพของเส้นใย และนอกเหนือจากสารตั้งต้นแล้ว ขั้นตอนนี้ยังช่วยแยกแยะผลิตภัณฑ์ของซัพพลายเออร์รายหนึ่งออกจากผลิตภัณฑ์ของคู่แข่งได้ดีที่สุด การยึดเกาะระหว่างสารประกอบอินทรีย์เมทริกซ์และเส้นใยคาร์บอนจึงมีความจำเป็นต่อการเสริมความแข็งแรงให้กับคอมโพสิต ตลอดขั้นตอนการผลิตเส้นใยคาร์บอน จะมีการเคลือบผิวเพื่อเพิ่มการยึดเกาะนี้
เวลาโพสต์: 01-11-2018