La fibra de carbono, compuesta por combinaciones de materiales diferentes (fibra y resina), su variabilidad y, por lo tanto, su adaptabilidad, son fundamentales para su atractivo. Como sustituto del metal, los compuestos de fibra de carbono ofrecen diez veces la resistencia del acero. Los fabricantes de fibra de carbono crean productos similares, pero no idénticos. La fibra de carbono varía en módulo de tracción (o rigidez determinada como deformación bajo tensión) y resistencia a la tracción, la compresión y la fatiga.
La fibra de carbono basada en PAN está disponible actualmente en módulo bajo (menos de treinta y dos millones de lbf/in² o Msi), módulo estándar (de 33 a 36 Msi), módulo intermedio (de 40 a 50 Msi), módulo alto (de 50 a 70 Msi) y módulo ultraalto (de 70 a 140 Msi).
En términos más simples, la fibra de carbono se crea mediante el desplazamiento de una fibra precursora orgánica en una atmósfera inerte a temperaturas superiores a 982,22 °C (1800 °F). Sin embargo, la fabricación de fibra de carbono puede ser una tarea compleja.
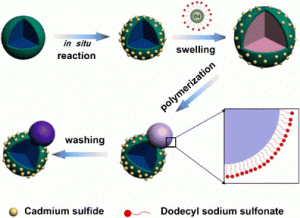
Polimerización e hilado
Polimerización
El proceso comienza con una materia prima química, denominada precursor, que contiene la estructura molecular de la fibra. Actualmente, casi el 100 % de la fibra de carbono producida se fabrica con precursores a base de tela o brea; sin embargo, la mayor parte proviene del poliacrilonitrilo (PAN), fabricado a partir de nitrito, y el nitrito proviene de los productos químicos industriales propano y amoníaco.
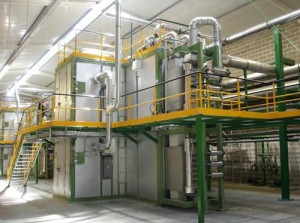
Oxidación y carbonización
Oxidación
Estas bobinas se cargan en la cesta y, durante la etapa de oxidación, la más larga de la producción, las fibras de PAN se alimentan a través de una serie de hornos dedicados. Antes de entrar en el aparato principal, las fibras de PAN se compactan formando una estopa o lámina llamada urdimbre. La temperatura de la cámara oscila entre los 200 °C (392 °F) y los 300 °C (572 °F).
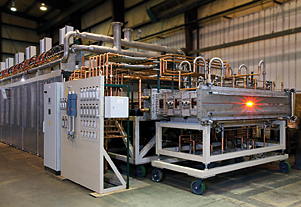
Tratamiento de superficies y dimensionamiento
Tratamiento de superficies y dimensionamiento
El siguiente paso es esencial para el rendimiento de la fibra y, además de los precursores, es el que mejor distingue el producto de un proveedor del de la competencia. La adhesión entre el compuesto orgánico de la matriz y las fibras de carbono es esencial para reforzar el compuesto; durante el proceso de producción de la fibra de carbono, se aplica un tratamiento superficial para mejorar esta adhesión.
Hora de publicación: 01-nov-2018