Uhlíkové vlákna, zložené z kombinácií rôznych materiálov (vlákna a živice), ich variabilita a teda prispôsobiteľnosť sú kľúčové pre ich šarm. Ako náhrada kovu poskytujú kompozity z uhlíkových vlákien desaťkrát väčšiu pevnosť ako oceľ. Výrobcovia uhlíkových vlákien vytvárajú produkty, ktoré sú síce podobné, ale nie identické. Uhlíkové vlákna sa líšia modulom ťahu (alebo tuhosťou určenou ako deformácia pod napätím) a pevnosťou v ťahu, tlaku a únave.
Uhlíkové vlákna na báze PAN sú v súčasnosti dostupné s nízkym modulom (menej ako 32 miliónov lbf/in² alebo Msi), bežným modulom (33 až 36 Msi), stredným modulom (40 až 50 Msi), vysokým modulom (50 až 70 Msi) a ultravysokým modulom (70 až 140 Msi).
Najjednoduchšie povedané, uhlíkové vlákno sa vytvára presunom organického prekurzorového vlákna s pridruženým stupňom v inertnej atmosfére s pridruženým stupňom pri teplotách vyšších ako 982,22 °C. Výroba uhlíkových vlákien však môže byť pokročilým odvetvím.
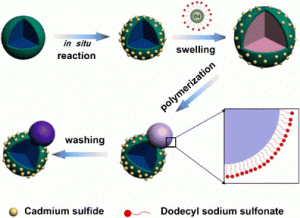
Polymerizácia a spriadanie
Polymerizácia
Proces začína chemickou zmesou vstupných surovín nazývanou prekurzor, ktorý má molekulárnu kostru vlákna. V súčasnosti sa približne 100 percent vyrobených uhlíkových vlákien vyrába z prekurzorov na báze tkaniny alebo smoly, avšak väčšina z nich pochádza z polyakrylonitrilu (PAN), ktorý sa vyrába z dusitanov, a dusitany pochádzajú z priemyselných chemikálií propánu a amoniaku.
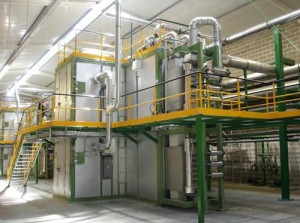
Oxidácia a karbonizácia
Oxidácia
Tieto cievky sa vložia do koša a počas najdlhšej výrobnej, oxidačnej fázy, sa vlákna PAN prevedú sériou špecializovaných pecí. Predtým, ako vstúpia do hlavného kuchynského spotrebiča, sa vlákna PAN zvinú do kúdele alebo listu nazývaného osnova. Teplota komory sa pohybuje od cca 200 °C do 300 °C.
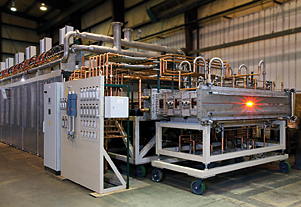
Povrchová úprava a glejenie
Povrchová úprava a glejenie
Ďalší krok je nevyhnutný pre výkonnosť vlákien a okrem prekurzorov najlepšie odlišuje produkt jedného dodávateľa od produktu konkurencie. Adhézia medzi matricovou organickou zlúčeninou a teda uhlíkovými vláknami je nevyhnutná pre vystuženie kompozitu; počas celého procesu výroby uhlíkových vlákien sa vykonáva povrchová úprava na zvýšenie tejto adhézie.
Čas uverejnenia: 1. novembra 2018