A fibra de carbono, composta por combinações de materiais diferentes (fibra e resina), tem sua variabilidade e, portanto, sua adaptabilidade, como elementos centrais para seu charme. Como substituto do metal, os compósitos de fibra de carbono oferecem dez vezes a resistência do aço. Os fabricantes de fibra de carbono criam produtos semelhantes, mas não idênticos. A fibra de carbono varia em módulo de tração (ou rigidez, definida como deformação sob tensão) e resistência à tração, compressão e fadiga.
A fibra de carbono baseada em PAN está disponível atualmente em módulo baixo (menos de trinta e dois milhões de lbf/in² ou Msi), módulo padrão (33 a trinta e seis Msi), módulo intermediário (40 a cinquenta Msi), módulo alto (50 a setenta Msi) e módulo ultra-alto (70 a cento e quarenta Msi).
Em termos mais simples, a fibra de carbono é criada pela transferência de uma fibra precursora orgânica em uma atmosfera inerte a temperaturas superiores a 982,22 °C (1800 °F). A fabricação de fibra de carbono, no entanto, é um empreendimento avançado.
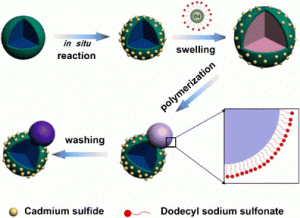
Polimerização e Fiação
Polimerização
O processo começa com uma matéria-prima composta química, denominada precursor, que contém a estrutura molecular da fibra. Hoje, cerca de 100% da fibra de carbono produzida é feita de tecido ou precursores à base de piche, mas a maior parte vem de poliacrilonitrila (PAN), fabricada a partir de nitrito, e o nitrito vem dos produtos químicos industriais propano e amônia.
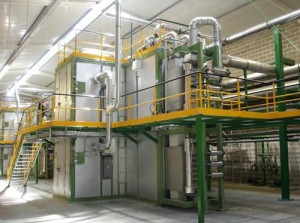
Oxidação e Carbonização
Oxidação
Essas bobinas são carregadas na cesta e, durante a fase mais longa de produção, a oxidação, as fibras de PAN são alimentadas por uma série de fornos dedicados. Antes de entrarem no eletrodoméstico principal, as fibras de PAN são acondicionadas em uma estopa ou folha chamada urdume. A temperatura da câmara varia de aproximadamente 200 °C (392 °F) a 300 °C (572 °F).
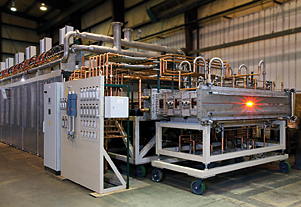
Tratamento de superfície e dimensionamento
Tratamento de superfície e dimensionamento
A próxima etapa é essencial para o desempenho da fibra e, além dos precursores, distingue melhor o produto de um fornecedor do produto da concorrência. A adesão entre o composto orgânico da matriz e as fibras de carbono é essencial para o reforço do compósito; durante o processo de produção da fibra de carbono, é realizado um tratamento de superfície para aumentar essa adesão.
Horário da postagem: 01/11/2018