Fibra de carbon, compusă din combinații de materiale diferite (fibră și rășină), variabilitatea acesteia și, prin urmare, adaptabilitatea, sunt esențiale pentru farmecul lor. Ca înlocuitori de metal, compozitele din fibră de carbon oferă o rezistență de zece ori mai mare decât oțelul. Producătorii de fibră de carbon creează produse similare, dar nu identice. Fibra de carbon variază în ceea ce privește modulul de tracțiune (sau rigiditatea determinată ca deformare sub deformare) și rezistența la tracțiune, compresie și oboseală.
Fibra de carbon pe bază de PAN este disponibilă astăzi cu modul scăzut (mai puțin de 32 de milioane lbf/in² sau Msi), modul obișnuit (33 până la 36 Msi), modul intermediar (40 până la 50 Msi), modul ridicat (50 până la 70 Msi) și modul ultra-înalt (70 până la 140 Msi).
În termeni simpli, fibra de carbon este creată prin depunerea fibrei precursoare organice într-o atmosferă inertă la temperaturi mai mari de 982,22 °C (1800 °F). Fabricarea fibrei de carbon, însă, poate fi o întreprindere complexă.
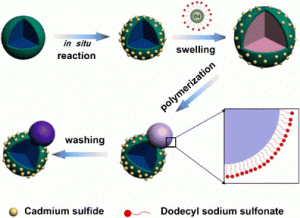
Polimerizare și filare
Polimerizare
Procesul începe cu un compus chimic de alimentare, denumit precursor, care are coloana moleculară a fibrei. Astăzi, aproximativ 100% din fibra de carbon creată este fabricată din precursori pe bază de țesătură sau smoală, însă cea mai mare parte provine din poliacrilonitril (PAN), fabricat din nitriți, iar nitriții provin din substanțele chimice industriale propan și amoniac.
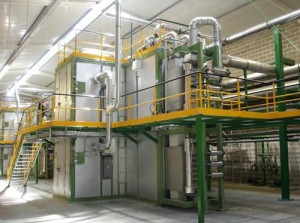
Oxidare și carbonizare
Oxidare
Aceste bobine sunt încărcate în coș, iar în cea mai lungă etapă de producție, cea de oxidare, fibrele PAN sunt alimentate printr-o serie de cuptoare dedicate. Înainte de a intra în aparatul principal de bucătărie, fibrele PAN se îmbină într-un cablu sau o foaie numită urzeală. Temperatura camerei variază de la 392 °F (aproximativ 200 °C) la 572 °F (300 de grade Celsius).
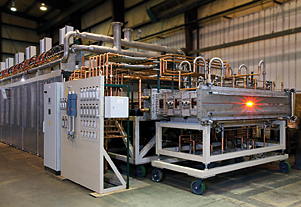
Tratarea suprafeței și dimensionarea
Tratarea suprafeței și dimensionarea
Următorul pas este esențial pentru performanța fibrei și, pe lângă precursori, este cel care distinge cel mai bine produsul unui furnizor de cel al concurenței. Aderența dintre compusul organic al matricei și, prin urmare, fibrele de carbon este esențială pentru armarea compozitului; pe parcursul procesului de producere a fibrei de carbon, se efectuează un tratament de suprafață pentru a spori această aderență.
Data publicării: 01 noiembrie 2018