A fibra de carbono, composta por combinacións de materiais diferentes (fibra e resina), a súa variabilidade e, polo tanto, a súa capacidade de adaptación son fundamentais para o seu encanto. Como substitutos do metal, os compostos de fibra de carbono ofrecen dez veces a resistencia do aceiro. Os fabricantes de fibra de carbono crean produtos similares pero non idénticos. A fibra de carbono varía en módulo de tracción (ou rixidez determinada como deformación baixo tensión) e resistencia á tracción, compresión e fatiga.
A fibra de carbono baseada en PAN está dispoñible hoxe en día en módulo baixo (menos de trinta e dous millóns de lbf/in² ou Msi), módulo estándar (de 33 a 36 Msi), módulo intermedio (de 40 a 50 Msi), módulo alto (de 50 a 70 Msi) e módulo ultraalto (de 70 a 140 Msi).
En termos máis sinxelos, a fibra de carbono créase mediante o cambio de fibra precursora orgánica de grao asociado nunha atmosfera inerte a temperaturas superiores a 1800 °F (982,22 °C). Non obstante, a fabricación de fibra de carbono pode ser unha empresa complexa.
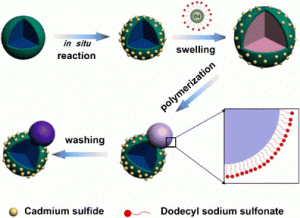
Polimerización e fiación
Polimerización
O proceso comeza cun composto químico de alimentación denominado precursor que contén a columna vertebral molecular da fibra. Hoxe en día, arredor do 100 % da fibra de carbono creada provén de precursores a base de tea ou brea, pero a maior parte provén do poliacrilonitrilo (PAN), fabricado a partir de nitrito, e o nitrito provén dos produtos químicos industriais propano e amoníaco.
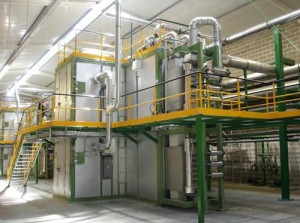
Oxidación e carbonización
Oxidación
Estas bobinas cárganse na cesta e, na fase de produción máis longa, a de oxidación, as fibras de PAN aliméntanse a través dunha serie de fornos dedicados. Antes de entrar no electrodoméstico principal da cociña, as fibras de PAN acomodanse nun halo ou folla chamada urdime. A temperatura da cámara oscila entre os 200 °C e os 300 graos Celsius.
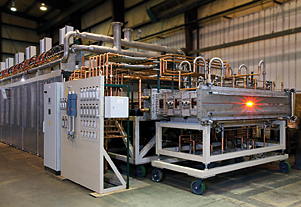
Tratamento superficial e dimensionamento
Tratamento superficial e dimensionamento
O seguinte paso é esencial para o rendemento da fibra e, ademais dos precursores, é o que mellor distingue o produto dun provedor do produto da competencia. A adhesión entre o composto orgánico da matriz e, polo tanto, as fibras de carbono son esenciais para reforzar o composto; durante todo o método de produción de fibra de carbono, realízase un tratamento superficial para impulsar esta adhesión.
Data de publicación: 01-11-2018