Въглеродните влакна, съставени от комбинации от различни материали (влакна и смола), тяхната вариативност и следователно възможност за персонализиране са от основно значение за техния чар. Като заместител на метала, композитите от въглеродни влакна осигуряват десет пъти по-голяма здравина от стоманата. Производителите на въглеродни влакна създават продукти, които са подобни, но не идентични. Въглеродните влакна се различават по модул на опън (или твърдост, определена като деформация под напрежение), както и по якост на опън, натиск и умора.
В днешно време въглеродните влакна на базата на PAN се предлагат с нисък модул (под тридесет и два милиона lbf/in² или Msi), стандартен модул (от 33 до тридесет и шест Msi), среден модул (от 40 до 50 Msi), висок модул (от 50 до 70 Msi) и ултрависок модул (от 70 до 140 Msi).
Най-просто казано, въглеродните влакна се създават чрез преобразуване на органични прекурсорни влакна с асоциирана степен в инертна атмосфера с асоциирана степен при температури по-високи от 1800°F (982,22 °C). Производството на въглеродни влакна обаче може да бъде сложна дейност.
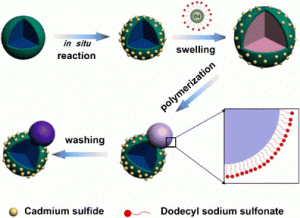
Полимеризация и предене
Полимеризация
Процесът започва с химическа смес, наречена прекурсор, която има молекулярната основа на влакното. Днес около 100 процента от произведените въглеродни влакна са направени от прекурсори на базата на плат или смола, но по-голямата част от тях идват от полиакрилонитрил (PAN), произведен от нитрит, а нитритът идва от промишлените химикали пропан и амоняк.
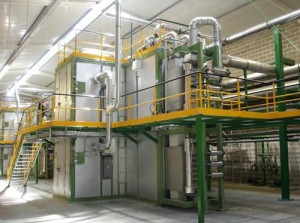
Окисление и карбонизация
Окисление
Тези бобини се зареждат в кошницата и в рамките на най-дългия производствен етап, етап на окисление, PAN влакната преминават през серия от специални пещи. Преди да влязат в основния кухненски уред, PAN влакната се оформят в кълчище или лист, наречен основа. Температурата в камерата варира от около 200°C до 300°C.
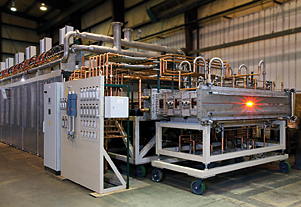
Повърхностна обработка и оразмеряване
Повърхностна обработка и оразмеряване
Следващата стъпка е от съществено значение за производителността на влакната и освен прекурсорите, тя най-добре отличава продукта на един доставчик от продукта на конкурентите. Адхезията между матричното органично съединение и следователно въглеродните влакна е от съществено значение за подсилване на композита; по време на целия процес на производство на въглеродни влакна се извършва повърхностна обработка, за да се подобри тази адхезия.
Време на публикуване: 01 ноември 2018 г.