Włókno węglowe, składające się z kombinacji różnych materiałów (włókna i żywicy), ich zmienność, a zatem możliwość dostosowania, są kluczowe dla ich uroku. Jako zamiennik metalu, kompozyty z włókna węglowego zapewniają dziesięciokrotnie większą wytrzymałość niż stal. Producenci włókna węglowego tworzą produkty, które są podobne, ale nie identyczne. Włókno węglowe różni się modułem rozciągania (lub sztywnością określaną jako odkształcenie poniżej odkształcenia) oraz wytrzymałością na rozciąganie, ściskanie i zmęczenie.
Włókno węglowe na bazie PAN jest obecnie dostępne w wersjach o niskim module (mniej niż trzydzieści dwa miliony lbf/in² lub Msi), zwykłym module (od 33 do trzydziestu sześciu Msi), module pośrednim (od 40 do pięćdziesięciu Msi), wysokim module (od 50 do siedemdziesięciu Msi) i ultrawysokim module (od 70 do 140 Msi).
Najprościej rzecz ujmując, włókno węglowe powstaje w wyniku przesunięcia organicznego włókna prekursorowego w atmosferze obojętnej w temperaturach wyższych niż 1800°F (982,22 °C). Produkcja włókna węglowego może być jednak zaawansowanym przedsięwzięciem.
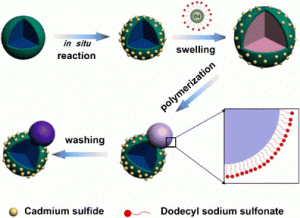
Polimeryzacja i przędzenie
Polimeryzacja
Proces zaczyna się od surowca chemicznego, zwanego prekursorem, który ma molekularny szkielet włókna. Obecnie około 100 procent wytwarzanego włókna węglowego powstaje z prekursorów na bazie tkaniny lub smoły, jednak większość z nich pochodzi z poliakrylonitrylu (PAN), wytwarzanego z azotynu, a azotyn pochodzi z przemysłowych środków chemicznych propanu i amoniaku.
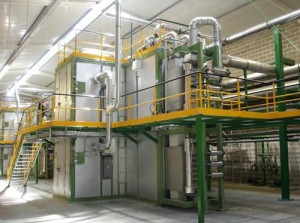
Utlenianie i karbonizacja
Utlenianie
Te szpule są ładowane do kosza, a w najdłuższym etapie produkcji, etapie utleniania, włókna PAN są podawane przez szereg dedykowanych pieców. Zanim trafią do głównego urządzenia kuchennego, włókna PAN są układane w pasmo lub arkusz zwany osnową. Temperatura komory waha się od 392 °F (ok. 200 °C) do 572 °F (300 stopni Celsjusza).
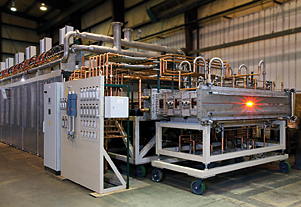
Obróbka powierzchni i kalibrowanie
Obróbka powierzchni i kalibrowanie
Następny krok jest niezbędny dla wydajności włókien, a dodatkowo do prekursorów, najlepiej odróżnia produkt jednego dostawcy od produktu konkurencji. Przyczepność między organicznym związkiem matrycy a włóknami węglowymi jest niezbędna do wzmocnienia kompozytu; w całej metodzie produkcji włókien węglowych przeprowadza się obróbkę powierzchni w celu zwiększenia tej przyczepności.
Czas publikacji: 01-11-2018