Kohlenstofffasern sind anorganische Polymerfasern, ein neuartiges anorganisches Material mit einem Kohlenstoffgehalt von über 95 %. Sie zeichnen sich durch geringe Dichte, hohe Festigkeit, hohe Temperaturbeständigkeit, hohe chemische Stabilität, Ermüdungsbeständigkeit, Verschleißfestigkeit und weitere hervorragende physikalische und chemische Eigenschaften aus. Sie zeichnen sich durch hohe Schwingungsdämpfung, gute Wärmeleitfähigkeit, elektromagnetische Abschirmung und einen niedrigen Wärmeausdehnungskoeffizienten aus. Aufgrund dieser hervorragenden Eigenschaften finden Kohlenstofffasern breite Anwendung in der Luft- und Raumfahrt, im Schienenverkehr, im Fahrzeugbau, in der Waffen- und Ausrüstungsindustrie, in Baumaschinen, im Infrastrukturbau, im Schiffsbau, in der Erdöltechnik, in der Windenergie, in der Sportartikelindustrie und anderen Bereichen.
Aufgrund des nationalen strategischen Bedarfs an Kohlefaserwerkstoffen zählt China diese zu den Kerntechnologien der aufstrebenden Industrien, die besonders gefördert werden. Im nationalen Wissenschafts- und Technologieplan „Zwölf Fünf“ zählt die Herstellungs- und Anwendungstechnologie von Hochleistungskohlenstofffasern zu den Kerntechnologien der staatlich geförderten strategischen aufstrebenden Industrien. Im Mai 2015 veröffentlichte der Staatsrat offiziell „Made in China 2025“. Neue Werkstoffe werden als Schlüsselbereiche intensiv gefördert und entwickelt, darunter Hochleistungsstrukturwerkstoffe und fortschrittliche Verbundwerkstoffe. Im Oktober 2015 veröffentlichte das Ministerium für Industrie und Informationswirtschaft offiziell die „China Manufacturing 2025 Key Areas Technology Roadmap“. „Hochleistungsfasern und ihre Verbundwerkstoffe“ gelten als strategisches Schlüsselmaterial. Das Ziel für 2020 lautet, dass heimische Kohlefaserverbundwerkstoffe die technischen Anforderungen von Großflugzeugen und anderen wichtigen Geräten erfüllen. Im November 2016 veröffentlichte der Staatsrat den Nationalen Strategischen Entwicklungsplan für aufstrebende Industrien „Dreizehn Fünf“. Darin wird klar darauf hingewiesen, die Zusammenarbeit in der vor- und nachgelagerten Industrie für neue Materialien zu stärken, Pilotprojekte für kollaborative Anwendungen in Bereichen wie Kohlenstofffaserverbundwerkstoffen durchzuführen und eine Plattform für kollaborative Anwendungen aufzubauen. Im Januar 2017 formulierten das Ministerium für Industrie und Entwicklung, die NDRC, Wissenschaft und Technologie sowie das Finanzministerium gemeinsam den „Leitfaden für die Entwicklung neuer Materialindustrien“. Darin wird vorgeschlagen, bis 2020 „mehr als 70 wichtige neue Materialien in Bereichen wie Kohlenstofffaserverbundwerkstoffen, hochwertigem Spezialstahl und modernen Leichtmetallen zu industrialisieren und anzuwenden. Außerdem soll ein Unterstützungssystem für Prozessausrüstung aufgebaut werden, das dem Entwicklungsstand der chinesischen Industrie für neue Materialien entspricht.“
Da Kohlefasern und ihre Verbundwerkstoffe eine wichtige Rolle für die Landesverteidigung und die Lebensgrundlage der Bevölkerung spielen, konzentrieren sich viele Experten auf ihre Entwicklung und analysieren Forschungstrends. Dr. Zhou Hong überprüfte die wissenschaftlichen und technologischen Beiträge amerikanischer Wissenschaftler in den frühen Phasen der Entwicklung der Hochleistungs-Kohlefasertechnologie und analysierte und berichtete über 16 Hauptanwendungen und aktuelle technologische Fortschritte von Kohlefasern. Dr. Wei Xin überprüfte die Produktionstechnologie, Eigenschaften und Anwendung von Polyacrylnitril-Kohlefasern und ihre aktuelle technologische Entwicklung und machte einige konstruktive Vorschläge für die bestehenden Probleme bei der Entwicklung von Kohlefasern in China. Zudem haben viele Menschen Forschungen zur messtechnischen Analyse von Dokumenten und Patenten auf dem Gebiet der Kohlefasern und ihrer Verbundwerkstoffe durchgeführt. Beispielsweise haben Ma Xianglin und andere die Verteilung und Anwendung von Kohlefaserpatenten zwischen 1998 und 2017 aus messtechnischer Sicht analysiert. Yang Sisi und andere führen eine globale Patentrecherche und Datenstatistik zu Kohlenstofffasergeweben auf Grundlage der Innography-Plattform durch und analysieren dabei die jährlichen Entwicklungstrends von Patenten und Patentinhabern, die Hotspots der Patenttechnologie und die Kernpatente der Technologie.
Chinas Forschung im Bereich Carbonfasern verläuft nahezu synchron mit der Welt, entwickelt sich jedoch langsam. Die Produktion von Hochleistungs-Carbonfasern weist im Vergleich zum Ausland einen Rückstand auf. Daher ist es dringend erforderlich, den Forschungs- und Entwicklungsprozess zu beschleunigen, die strategische Ausrichtung zu verbessern und zukünftige Entwicklungschancen der Branche zu nutzen. Daher untersucht diese Arbeit zunächst die Projektausrichtung der Länder im Bereich Carbonfaserforschung, um die Forschungs- und Entwicklungsplanung in verschiedenen Ländern zu verstehen. Da die Grundlagenforschung und Anwendungsforschung im Bereich Carbonfasern für deren technische Forschung und Entwicklung von großer Bedeutung ist, werden parallel dazu wissenschaftliche Forschungsergebnisse (SCI-Veröffentlichungen) und angewandte Forschungsergebnisse (Patente) messtechnisch analysiert, um ein umfassendes Verständnis des Forschungs- und Entwicklungsfortschritts im Bereich Carbonfasern zu erlangen und die jüngsten Forschungsentwicklungen in diesem Bereich zu analysieren, um einen Einblick in den internationalen Forschungsfortschritt zu erhalten. Abschließend werden auf Grundlage der oben genannten Forschungsergebnisse einige Vorschläge für die Forschungs- und Entwicklungsstrategie im Bereich Carbonfasern in China unterbreitet.
2. CKohlenstofffaserForschungsprojektlayout vonwichtige Länder/Regionen
Zu den wichtigsten Produktionsländern für Kohlefaser zählen Japan, die USA, Südkorea, einige europäische Länder sowie Taiwan und China. Hochtechnologieländer haben bereits in der Frühphase der Entwicklung der Kohlefasertechnologie die Bedeutung dieses Materials erkannt, strategische Pläne umgesetzt und die Entwicklung von Kohlefasermaterialien energisch vorangetrieben.
2.1 Japan
Japan ist das am weitesten entwickelte Land in der Kohlefasertechnologie. Die drei japanischen Unternehmen Toray, Bong und Mitsubishi Liyang decken weltweit etwa 70 bis 80 % des Kohlefasermarktes ab. Dennoch legt Japan großen Wert darauf, seine Stärken in diesem Bereich zu erhalten, insbesondere die Entwicklung leistungsstarker panbasierter Kohlefasern sowie energie- und umweltfreundlicher Technologien mit starker personeller und finanzieller Unterstützung. Grundsatzpolitische Maßnahmen wie der Energiegrundplan, die strategischen Leitlinien für Wirtschaftswachstum und das Kyoto-Protokoll haben dies zu einem strategischen Projekt gemacht, das vorangetrieben werden sollte. Basierend auf der nationalen Energie- und Umweltpolitik hat das japanische Ministerium für Wirtschaft, Industrie und Eigentum das „Forschungs- und Entwicklungsprogramm für Energiespartechnologien“ aufgelegt. Dank dieser Maßnahmen konnte die japanische Kohlefaserindustrie alle Ressourcen effektiver zentralisieren und die Lösung gängiger Probleme der Kohlefaserindustrie vorantreiben.
Das Projekt „Technologieentwicklung wie innovative neue Strukturmaterialien“ (2013–2022) ist ein im Rahmen des Forschungsprojekts „Zukunftsentwicklung“ in Japan durchgeführtes Projekt, das die Entwicklung der erforderlichen innovativen Strukturmaterialtechnologien und die Kombination verschiedener Materialien deutlich vorantreiben soll. Das Hauptziel besteht darin, das Gewicht von Verkehrsmitteln zu reduzieren (um die Hälfte des Fahrzeuggewichts) und schließlich ihre praktische Anwendung zu realisieren. Nach der Übernahme des Forschungs- und Entwicklungsprojekts im Jahr 2014 entwickelte die Industrial Technology Development Agency (NEDO) mehrere Unterprojekte. Die Gesamtziele des Carbonfaser-Forschungsprojekts „Innovative Carbonfaser-Grundlagenforschung und -entwicklung“ waren: die Entwicklung neuer Carbonfaser-Vorläuferverbindungen, die Aufklärung des Bildungsmechanismus von Carbonisierungsstrukturen und die Entwicklung und Standardisierung von Bewertungsmethoden für Carbonfasern. Das von der Universität Tokio geleitete und gemeinsam mit dem Institute of Industrial Technology (NEDO), Toray, Teijin, Dongyuan und Mitsubishi Liyang durchgeführte Projekt hat im Januar 2016 bedeutende Fortschritte erzielt und stellt nach der Erfindung des „Kondo-Modus“ in Japan im Jahr 1959 einen weiteren wichtigen Durchbruch auf dem Gebiet der pfannenbasierten Kohlenstofffasern dar.
2.2 Vereinigte Staaten
Die US-amerikanische Verteidigungsforschungsagentur DARPA startete 2006 das Projekt „Advanced Structural Fiber“ mit dem Ziel, die führende wissenschaftliche Forschungskraft des Landes zu bündeln, um Strukturfasern der nächsten Generation auf Basis von Kohlenstofffasern zu entwickeln. Unterstützt durch dieses Projekt gelang dem Forschungsteam des Georgia Institute of Technology in den USA 2015 ein Durchbruch bei der Rohdrahtaufbereitungstechnologie, wodurch der Elastizitätsmodul um 30 % gesteigert werden konnte. Damit verfügen die USA über die Entwicklungskapazität für die dritte Generation von Kohlenstofffasern.
Im Jahr 2014 kündigte das US-Energieministerium (DOE) eine Subvention in Höhe von 11,3 Millionen Dollar für zwei Projekte an, die sich mit „mehrstufigen katalytischen Prozessen zur Umwandlung von nicht essbarem Biomassezucker in Acrylnitril“ und „Forschung und Optimierung von aus der Biomasseproduktion gewonnenem Acrylnitril“ befassen, um die Verwendung landwirtschaftlicher Rückstände zu fördern. Außerdem werden Forschungen zu kostengünstigen, erneuerbaren Hochleistungskohlenstofffasermaterialien für die Produktion erneuerbarer, nicht auf Lebensmitteln basierender Rohstoffe wie Holzbiomasse durchgeführt und es werden Pläne zur Senkung der Produktionskosten für erneuerbare Biomassekohlenstofffasern auf unter 5 USD/lb bis 2020 durchgeführt.
Im März 2017 kündigte das US-Energieministerium erneut eine Finanzierung von 3,74 Millionen Dollar für ein „Forschungs- und Entwicklungsprojekt für kostengünstige Kohlefaserkomponenten“ unter der Leitung des Western American Institute (WRI) an, dessen Schwerpunkt auf der Entwicklung kostengünstiger Kohlefaserkomponenten auf Basis von Ressourcen wie Kohle und Biomasse liegt.
Im Juli 2017 kündigte das US-Energieministerium die Bereitstellung von 19,4 Millionen Dollar für die Forschung und Entwicklung im Bereich der modernen energieeffizienten Fahrzeuge an. 6,7 Millionen Dollar davon fließen in die Herstellung kostengünstiger Kohlenstofffasern unter Verwendung computergestützter Materialien, einschließlich der Entwicklung mehrskaliger Bewertungsmethoden für integrierte Computertechnologie zur Beurteilung der Beliebtheit neuer Kohlenstofffaser-Vorläufer. Mithilfe fortschrittlicher molekulardynamischer Methoden, unterstützt durch Dichtefunktionaltheorie und maschinelles Lernen, werden hochmoderne Computertools entwickelt, um die Auswahleffizienz kostengünstiger Kohlenstofffaser-Rohstoffe zu verbessern.
2.3 Europa
Die europäische Kohlefaserindustrie entwickelte sich in den 1970er und 1980er Jahren des 20. Jahrhunderts in Japan und den USA. Aus technologischen und kapitalbedingten Gründen konnten jedoch viele einzelne Kohlefaserhersteller nicht mit der Hochphase der Nachfrage nach Kohlefasern nach 2000 Jahren Schritt halten und verschwanden. Das deutsche Unternehmen SGL ist das einzige europäische Unternehmen mit einem bedeutenden Anteil am weltweiten Kohlefasermarkt.
Im November 2011 startete die Europäische Union das Eucarbon-Projekt, dessen Ziel darin besteht, die europäischen Produktionskapazitäten für Kohlefasern und vorimprägnierte Materialien für die Luft- und Raumfahrt zu verbessern. Das Projekt dauerte vier Jahre und umfasste eine Gesamtinvestition von 3,2 Millionen Euro. Im Mai 2017 wurde Europas erste spezielle Kohlefaser-Produktionslinie für Weltraumanwendungen wie Satelliten erfolgreich in Betrieb genommen. Dadurch konnte Europa seine Importabhängigkeit bei diesem Produkt überwinden und die Sicherheit der Materialversorgung gewährleisten.
Das siebte EU-Rahmenprogramm soll das Projekt „Funktionale Kohlenstofffasern bei der Herstellung eines neuen Vorläufersystems mit kostengünstiger und handhabbarer Leistung“ (FIBRALSPEC) (2014–2017) mit 6,08 Millionen Euro unterstützen. Das auf vier Jahre angelegte Projekt unter der Leitung der Nationalen Technischen Universität Athen, Griechenland, mit Beteiligung multinationaler Unternehmen aus Italien, Großbritannien und der Ukraine konzentriert sich auf die Innovation und Verbesserung des Prozesses der kontinuierlichen Herstellung von Kohlenstofffasern auf Polyacrylnitrilbasis, um eine experimentelle Produktion von kontinuierlich panbasierten Kohlenstofffasern zu erreichen. Das Projekt hat die Entwicklung und Anwendung von Kohlenstofffasern und verbesserter Verbundtechnologie aus erneuerbaren organischen Polymerressourcen (wie Superkondensatoren, Notunterkünften sowie Prototypen mechanischer elektrischer Rotationsbeschichtungsmaschinen und die Entwicklung einer Produktionslinie für Nanofasern usw.) erfolgreich abgeschlossen.
Immer mehr Industriezweige, wie die Automobilindustrie, die Windkraft und der Schiffbau, benötigen leichte und leistungsstarke Verbundwerkstoffe. Dies stellt einen riesigen potenziellen Markt für die Kohlefaserindustrie dar. Die EU investiert 5,968 Millionen Euro in das Projekt Carboprec (2014–2017). Dessen strategisches Ziel ist die Entwicklung kostengünstiger Vorläufer aus in Europa weit verbreiteten erneuerbaren Materialien und die Verbesserung der Produktion von Hochleistungskohlenstofffasern durch Kohlenstoffnanoröhren.
Das Forschungsprogramm Cleansky II der Europäischen Union förderte 2017 das Projekt „Composite tire R&D“ unter der Leitung des Fraunhofer-Instituts für Produktions- und Systemzuverlässigkeit (LBF) in Deutschland. Ziel ist die Entwicklung von Vorderradkomponenten für kohlenstofffaserverstärkte Verbundwerkstoffe für den Airbus A320. Ziel ist eine Gewichtsreduzierung von 40 % im Vergleich zu herkömmlichen Metallwerkstoffen. Das Projekt wird mit rund 200.000 Euro gefördert.
2.4 Korea
Südkoreas Forschung und Entwicklung sowie die Industrialisierung von Carbonfasern begannen erst spät. Die Forschung und Entwicklung begann 2006 und trat 2013 offiziell in die Praxis um. Dadurch wurde die Abhängigkeit der koreanischen Carbonfasern von Importen umgekehrt. Die südkoreanische Xiaoxing Group und Taiguang Business als Branchenpioniere engagieren sich aktiv im Bereich der Carbonfaserindustrie und entwickeln sich dynamisch. Darüber hinaus hat die von Toray Japan in Korea gegründete Carbonfaserproduktionsbasis auch zum Carbonfasermarkt in Korea beigetragen.
Die koreanische Regierung hat beschlossen, die Xiaoxing Group zu einem Treffpunkt für innovative Carbonfaser-Industrien zu machen. Ziel ist die Bildung eines Carbonfaser-Industrieclusters, um die Entwicklung eines kreativen wirtschaftlichen Ökosystems in der gesamten Region Nordkorea zu fördern. Das ultimative Ziel ist die Schaffung einer zentralen Produktionskette vom Carbonfasermaterial über Komponenten bis hin zum fertigen Produkt. Der Aufbau eines Carbonfaser-Inkubationsclusters kann mit dem Silicon Valley in den USA verglichen werden, um neue Märkte zu erschließen und neue Wertschöpfung zu schaffen. Ziel ist es, bis 2020 den Export von Carbonfaserprodukten im Wert von 10 Milliarden US-Dollar (entspricht etwa 55,2 Milliarden Yuan) zu erreichen.
3. Analyse der globalen Carbonfaserforschung und der Forschungsergebnisse
In diesem Unterabschnitt werden die SCI-Dokumente zur Kohlefaserforschung und die DII-Patentergebnisse seit 2010 gezählt, um die akademische Forschung und die industrielle Forschung und Entwicklung der globalen Kohlefasertechnologie gleichzeitig zu analysieren und den Fortschritt der Kohlefaserforschung und -entwicklung auf internationaler Ebene vollständig zu verstehen.
Daten stammen aus der Scie-Datenbank und der Dewent-Datenbank in der von Clarivate Analytics veröffentlichten Web of Science-Datenbank; Abrufzeitraum: 2010–2017; Abrufdatum: 1. Februar 2018.
SCI-Papierabrufstrategie: Ts = ((Kohlefaser* oder Carbonfaser* oder („Kohlefaser*“ nicht „Kohlefaserglas“) oder „Kohlefaser*“ oder „Kohlefilament*“ oder ((Polyacrylnitril oder Pech) und „Vorläufer*“ und Faser*) oder („Graphitfaser*“)) nicht („Bambuskohlenstoff“))。
Dewent Patentsuchstrategie: Ti=((Kohlefaser* oder Kohlefaser* oder ("Kohlefaser*" nicht "Kohlefaser-Glasfaser") oder "Kohlefaser*" oder "Kohlefilament*" oder ((Polyacrylnitril oder Pech) und "Vorläufer*" und Faser*) oder ("Graphitfaser*")) nicht ("Bambuskohlenstoff")) oder TS=((Kohlefaser* oder Kohlefaser* oder ("Kohlefaser*" nicht "Kohlefaser-Glasfaser") oder "Kohlefaser*" oder "Kohlefilament*" oder ((Polyacrylnitril oder Pech) und "Vorläufer*" und Faser*) oder ("Graphitfaser*")) nicht ("Bambuskohlenstoff")) und IP=(D01F-009/12 oder D01F-009/127 oder D01F-009/133 oder D01F-009/14 oder D01F-009/145 oder D01F-009/15 oder D01F-009/155 oder D01F-009/16 oder D01F-009/17 oder D01F-009/18 oder D01F-009/20 oder D01F-009/21 oder D01F-009/22 oder D01F-009/24 oder D01F-009/26 oder D01F-09/28 oder D01F-009/30 oder D01F-009/32 oder C08K-007/02 oder C08J-005/04 oder C04B-035/83 oder D06M-014/36 oder D06M-101/40 oder D21H-013/50 oder H01H-001/027 oder H01R-039/24)。
3.1 Trend
Seit 2010 wurden weltweit 16.553 relevante Artikel veröffentlicht und 26.390 Erfindungspatente angemeldet. Dabei ist von Jahr zu Jahr ein stetiger Aufwärtstrend zu erkennen (Abbildung 1).
3.2 Länder- oder Regionenverteilung
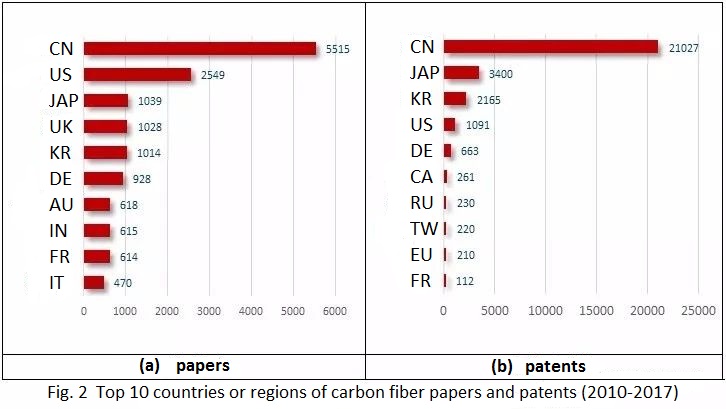
Die zehn Institutionen mit den meisten weltweiten Forschungsarbeiten zu Kohlenstofffasern stammen aus China. Die fünf führenden Institutionen sind: die Chinesische Akademie der Wissenschaften, das Harbin Institute of Technology, die Northwestern University of Technology, die Donghua University und das Beijing Institute of Aeronautics and Astronautics. Unter den ausländischen Institutionen belegen das Indian Institute of Technology, die Universität Tokio, die Universität Bristol, die Monash University, die Universität Manchester und das Georgia Institute of Technology die Plätze 10 bis 20 (Abb. 3).
Die Anzahl der Patentanmeldungen in den Top 30 Institutionen: Japan hat 5, und 3 davon sind unter den Top 5, Toray Company steht an erster Stelle, gefolgt von Mitsubishi Liyang (2.), Teijin (4.), East State (10.), Japan Toyo Textile Company (24.), China hat 21 Institutionen, Sinopec Group hat die größte Anzahl an Patenten und steht an dritter Stelle. An zweiter Stelle folgen Harbin Institute of Technology, Henan Ke Letter Cable Company, Donghua University, China Shanghai Petrochemical, Beijing Chemical Industry usw. Die Chinese Academy of Sciences Shanxi Coal hat 66 Erfindungspatente angemeldet und liegt damit auf Platz 27. Südkoreanische Institutionen haben 2, davon Xiaoxing Co., Ltd. steht an erster Stelle und liegt auf Platz 8.
Die Veröffentlichungen stammen hauptsächlich von Universitäten und wissenschaftlichen Forschungseinrichtungen, die Patente hauptsächlich von den Unternehmen. Daraus lässt sich erkennen, dass die Herstellung von Kohlefasern eine Hightech-Industrie ist. Als Hauptorgan der Entwicklung der Kohlefaser-Forschungs- und Entwicklungsindustrie legt das Unternehmen großen Wert auf den Schutz der Kohlefaser-Forschungs- und Entwicklungstechnologie. Insbesondere die beiden größten Unternehmen in Japan liegen bei der Anzahl der Patente weit vorn.
3.4 Forschungsschwerpunkte
Forschungsarbeiten zu Kohlefasern decken die meisten Forschungsthemen ab: Kohlefaserverbundwerkstoffe (einschließlich kohlenstofffaserverstärkter Verbundwerkstoffe, Polymermatrixverbundwerkstoffe usw.), Forschung zu mechanischen Eigenschaften, Finite-Elemente-Analyse, Kohlenstoffnanoröhren, Delamination, Verstärkung, Ermüdung, Mikrostruktur, elektrostatisches Spinnen, Oberflächenbehandlung, Adsorption usw. Arbeiten zu diesen Schlüsselwörtern machen 38,8 % der Gesamtanzahl der Arbeiten aus.
Patente für Erfindungen im Bereich Kohlefasern decken die meisten Bereiche der Kohlefaserherstellung, der Produktionsanlagen und der Verbundwerkstoffe ab. Unter ihnen sind die japanischen Unternehmen Toray, Mitsubishi Liyang und Teijin mit wichtigen technischen Patenten im Bereich „kohlenstofffaserverstärkte Polymerverbindungen“ vertreten. Darüber hinaus verfügen Toray und Mitsubishi Liyang über einen großen Anteil an Patenten im Bereich „Polyacrylnitril-Herstellung von Kohlefasern und Produktionsanlagen“, „Herstellung von Kohlefasern mit ungesättigten Nitrilen wie Polyacrylnitril und Polyvinylidencyanidethylen“ und anderen Technologien. Der größte Anteil der Patente liegt beim japanischen Unternehmen Teijin im Bereich „Kohlenstofffasern und Sauerstoffverbundwerkstoffe“.
Die China Sinopec Group, die Beijing Chemical University und die Chinese Academy of Sciences Ningbo Materials verfügen über einen großen Anteil an Patentanmeldungen im Bereich „Herstellung von Kohlenstofffasern aus Polyacrylnitril und Produktionsausrüstung“. Darüber hinaus haben die Beijing University of Chemical Engineering, das Shanxi Coal Chemical Institute der Chinese Academy of Sciences und die Chinese Academy of Sciences Ningbo Materials einen Schwerpunkt bei der Technologieanmeldung „Verwendung anorganischer Elementfasern als Bestandteile zur Herstellung von Polymerverbindungen“. Das Harbin Institute of Technology hat sich auf die Anmeldungen im Bereich „Behandlung von Kohlenstofffasern“, „Verbundwerkstoffe aus Kohlenstofffasern und sauerstoffhaltigen Verbindungen“ und anderen Technologien konzentriert.
Darüber hinaus geht aus der jährlichen statistischen Verteilungsstatistik globaler Patente hervor, dass in den letzten drei Jahren eine Reihe neuer Brennpunkte entstanden sind, wie etwa: „Zusammensetzungen aus Polyamiden, die durch Bildung einer Carboxylat-Bindungsreaktion in der Hauptkette erhalten werden“, „Polyesterzusammensetzungen aus der Bildung von 1-Carbonsäureester-Bindungen in der Hauptkette“, „Verbundwerkstoffe auf Basis synthetischer Materialien“, „zyklische Carbonsäuren, die Sauerstoffverbindungen als Bestandteile von Kohlenstofffaser-Verbundwerkstoffen enthalten“, „dreidimensionale Verfestigung oder Behandlung von Textilmaterialien“, „Herstellung von Polymerverbindungen aus ungesättigten Ethern, Acetalen, Halbacetalen, Ketonen oder Aldehyden ausschließlich durch die Reaktion ungesättigter Kohlenstoff-Kohlenstoff-Bindungen“, „adiabatische Materialrohre oder -kabel“, „Kohlenstofffaser-Verbundwerkstoffe mit Phosphatestern als Bestandteile“ und so weiter.
In den letzten Jahren hat die Forschung und Entwicklung im Bereich Kohlefasern stark zugenommen, wobei die meisten Durchbrüche in den USA und Japan erzielt wurden. Die neuesten Spitzentechnologien konzentrieren sich nicht nur auf die Herstellung und Aufbereitung von Kohlefasern, sondern auch auf Anwendungen in einem breiteren Spektrum von Automobilmaterialien, wie z. B. Leichtbau, 3D-Druck und Materialien zur Energieerzeugung. Darüber hinaus sind das Recycling und die Wiederverwertung von Kohlefasermaterialien, die Aufbereitung von Holzlignin-Kohlefasern und andere Errungenschaften herausragend. Die repräsentativen Ergebnisse sind im Folgenden beschrieben:
1) Das US-amerikanische Georgia Institute of Technology erzielt einen Durchbruch bei der Kohlefasertechnologie der dritten Generation
Im Juli 2015 gelang es dem Georgia Institute of Technology mit DARPA-Finanzierung, mit seiner innovativen, panbasierten Gel-Spinntechnik für Kohlefasern den Modul deutlich zu steigern und die Hershey IM7-Kohlefaser zu übertreffen, die heute in großem Umfang in Militärflugzeugen verwendet wird. Damit ist das Institut nach Japan das zweite Land der Welt, das die dritte Generation der Kohlefasertechnologie beherrscht.
Die Zugfestigkeit der von Kumarz hergestellten Gel-Spinn-Kohlefaser beträgt 5,5 bis 5,8 GPa, der Zugmodul liegt zwischen 354 und 375 GPa. „Diese Endlosfaser weist die höchste Festigkeit und den höchsten Elastizitätsmodul auf. Im Kurzfilamentbündel beträgt die Zugfestigkeit bis zu 12,1 GPa und entspricht damit der höchsten Polyacrylnitril-Kohlefaser.“
2) Elektromagnetische Wellenheiztechnologie
Nedo entwickelte 2014 eine elektromagnetische Wellenheiztechnologie. Die elektromagnetische Wellenkarbonisierungstechnologie bezeichnet die Verwendung elektromagnetischer Wellenheiztechnologie zur Karbonisierung von Fasern bei atmosphärischem Druck. Die erzielte Leistung der Kohlefaser entspricht im Wesentlichen der Leistung der durch Hochtemperaturerhitzung hergestellten Kohlefaser. Der Elastizitätsmodul kann über 240 GPA liegen, und die Bruchdehnung beträgt über 1,5 %. Dies ist weltweit ein erster Erfolg.
Das faserartige Material wird durch elektromagnetische Wellen karbonisiert, sodass die für die Hochtemperaturerhitzung verwendete Karbonisierungsofenanlage nicht mehr benötigt wird. Dieses Verfahren verkürzt nicht nur die Karbonisierungszeit, sondern senkt auch den Energieverbrauch und die CO2-Emissionen.
3) Feinsteuerung des Karbonisierungsprozesses
Im März 2014 gab Toray die erfolgreiche Entwicklung der T1100G-Kohlefaser bekannt. Toray nutzt die traditionelle Pfannenspinntechnologie, um den Karbonisierungsprozess präzise zu steuern, die Mikrostruktur der Kohlefaser im Nanometerbereich zu verbessern und die mikrokristalline Graphitausrichtung, die mikrokristalline Größe und Defekte in der Faser nach der Karbonisierung zu kontrollieren. Dadurch können Festigkeit und Elastizitätsmodul deutlich verbessert werden. Die Zugfestigkeit der T1100G beträgt 6,6 GPa und ist damit 12 % höher als die der T800. Der Elastizitätsmodul beträgt 324 GPa und ist damit um 10 % höher. Damit ist die Faser nun industriell einsetzbar.
4) Oberflächenbehandlungstechnologie
Teijin East State hat erfolgreich eine Plasma-Oberflächenbehandlungstechnologie entwickelt, mit der sich das Erscheinungsbild von Kohlefasern in Sekundenschnelle verändern lässt. Diese neue Technologie vereinfacht den gesamten Produktionsprozess erheblich und reduziert den Energieverbrauch im Vergleich zur bestehenden Oberflächenbehandlungstechnologie mit wässrigen Elektrolytlösungen um 50 %. Darüber hinaus verbesserte sich nach der Plasmabehandlung auch die Haftung von Fasern und Harzmatrix.
5) Untersuchung der Retentionsrate der Zugfestigkeit von Kohlenstofffasern in einer Graphitumgebung mit hohen Temperaturen
Ningbo Materials hat eine detaillierte Studie zur Prozessanalyse, Strukturforschung und Leistungsoptimierung von hochfesten und hochmoduligen Kohlefasern aus dem Inland erfolgreich durchgeführt. Dabei hat das Unternehmen insbesondere die Forschungsarbeit zur Beibehaltung der Zugfestigkeit von Kohlefasern in einer Graphitumgebung mit hohen Temperaturen durchgeführt. Zudem ist es kürzlich gelungen, hochfeste und hochmodulige Kohlefasern mit einer Zugfestigkeit von 5,24 GPa und einem Zugmodulvolumen von 593 GPa herzustellen. Im Vergleich zu den hochfesten, hochgeformten Kohlefasern Toray m60j aus Japan (Zugfestigkeit 3,92 GPa, Zugmodul 588 GPa) weist diese Faser weiterhin einen Vorteil hinsichtlich der Zugfestigkeit auf.
6) Mikrowellengraphit
Yongda Advanced Materials hat die von den USA exklusiv patentierte Ultrahochtemperatur-Graphittechnologie erfolgreich entwickelt und damit die Produktion von mittel- und höherwertigen Kohlenstofffasern ermöglicht. Damit wurden drei Engpässe bei der Entwicklung hochwertiger Kohlenstofffasern überwunden: Die teuren Graphitanlagen unterliegen internationaler Kontrolle, die Schwierigkeiten bei der Rohseidenchemie sowie die niedrigen Produktionserträge und hohen Kosten. Bisher hat Yongda drei Arten von Kohlenstofffasern entwickelt, die die Festigkeit und den Elastizitätsmodul der ursprünglichen, relativ minderwertigen Kohlenstofffasern deutlich steigern.
7) Neues Verfahren zum Schmelzspinnen von panbasiertem Kohlenstofffaser-Rohdraht durch Fraunhofer, Deutschland
Das Fraunhofer-Institut für Angewandte Polymerforschung (IAP) gab kürzlich bekannt, dass es auf der Berliner Luftfahrtausstellung (ILA) vom 25. bis 29. April 2018 die neueste Comcarbon-Technologie vorstellen wird. Diese Technologie reduziert die Produktionskosten für massenproduzierte Kohlefasern erheblich.
Abb. 4 Rohdrahtschmelzspinnen.
Bekanntlich entfällt bei herkömmlichen Verfahren die Hälfte der Produktionskosten für panbasierte Kohlenstofffasern auf die Rohdrahtherstellung. Da der Rohdraht nicht schmelzbar ist, muss er in einem teuren Lösungsspinnverfahren (Solution Spinning) hergestellt werden. „Deshalb haben wir ein neues Verfahren zur Herstellung von panbasierter Rohseide entwickelt, das die Produktionskosten für Rohdraht um 60 % senken kann. Es handelt sich um ein wirtschaftliches und praktikables Schmelzspinnverfahren unter Verwendung eines speziell entwickelten schmelzbaren panbasierten Copolymers“, erklärt Dr. Johannes Ganster, Leiter der Abteilung für biologische Polymere am Fraunhofer IAP.
8) Plasmaoxidationstechnologie
4M Carbon Fiber gab bekannt, dass das Unternehmen die Plasmaoxidationstechnologie strategisch einsetzen wird, um hochwertige und kostengünstige Carbonfasern herzustellen und zu vertreiben, und nicht nur Lizenzen für die Technologie vergeben wird. 4M gibt an, dass die Plasmaoxidationstechnologie dreimal schneller als herkömmliche Oxidationstechnologien ist und dabei weniger als ein Drittel der Energie verbraucht. Diese Aussagen werden von vielen internationalen Carbonfaserherstellern bestätigt, die sich mit einigen der weltweit größten Carbonfaserhersteller und Automobilhersteller beraten, um die Produktion kostengünstiger Carbonfasern voranzutreiben.
9) Zellulose-Nanofaser
Die japanische Universität Kyoto arbeitet gemeinsam mit mehreren großen Zulieferern wie dem Elektroinstallationsunternehmen (Toyotas größtem Zulieferer) und der Daikyonishikawa Corp. an der Entwicklung von Kunststoffen, die Zellulose-Nanofasern enthalten. Dieses Material wird durch Zerkleinern von Holzzellstoff in wenige Mikrometer (1 pro tausend Millimeter) hergestellt. Das Gewicht des neuen Materials beträgt nur ein Fünftel des Stahlgewichts, seine Festigkeit ist jedoch fünfmal so hoch wie die von Stahl.
10) Carbonfaser-Frontkörper aus Polyolefin- und Lignin-Rohstoffen
Das Oak Ridge National Laboratory in den USA arbeitet seit 2007 an der kostengünstigen Kohlefaserforschung und hat Kohlefaser-Frontkörper für Polyolefin- und Lignin-Rohstoffe sowie fortschrittliche Technologien zur Plasma-Voroxidation und Mikrowellenkarbonisierung entwickelt.
11) Das neue Polymer (Vorläuferpolymer) wurde durch Entfernen der feuerfesten Behandlung entwickelt
Bei einem von der Universität Tokio geleiteten Herstellungsverfahren wurde ein neues Polymer (Vorläuferpolymer) entwickelt, bei dem die Feuerfestbehandlung entfällt. Der springende Punkt ist, dass das Polymer nach dem Spinnen zu Seide nicht der ursprünglichen Feuerfestbehandlung unterzogen wird, sondern im Lösungsmittel oxidiert wird. Zur Karbonisierung wird es dann in einem Mikrowellengerät auf über 1.000 °C erhitzt. Das Aufheizen dauert nur 2–3 Minuten. Nach der Karbonisierungsbehandlung wird Plasma auch zur Oberflächenbehandlung verwendet, sodass Kohlenstofffasern hergestellt werden können. Die Plasmabehandlung dauert weniger als 2 Minuten. Auf diese Weise kann die ursprüngliche Sinterzeit von 30–60 Minuten auf etwa 5 Minuten reduziert werden. Bei dem neuen Herstellungsverfahren wird die Plasmabehandlung durchgeführt, um die Bindung zwischen Kohlenstofffasern und thermoplastischem Harz als CFK-Basismaterial zu verbessern. Der Zugelastizitätsmodul der mit dem neuen Herstellungsverfahren hergestellten Kohlenstofffasern beträgt 240 GPa, die Zugfestigkeit 3,5 GPa und die Dehnung erreicht 1,5 %. Diese Werte liegen auf dem gleichen Niveau wie die für Sportartikel etc. verwendete Toray Universal Grade Carbonfaser T300.
12) Recycling und Nutzung von Kohlenstofffasermaterialien im Wirbelschichtverfahren
Mengran Meng, Erstautor der Studie, erklärte: „Die Rückgewinnung von Kohlenstofffasern reduziert die Umweltbelastung im Vergleich zur Rohproduktion von Kohlenstofffasern. Allerdings ist das Bewusstsein für potenzielle Recyclingtechnologien und die wirtschaftliche Machbarkeit der Nutzung von recycelten Kohlenstofffasern begrenzt.“ Das Recycling erfolgt in zwei Schritten: Zunächst müssen die Fasern aus den Kohlenstofffaserverbundstoffen gewonnen und durch mechanisches Mahlen, Pyrolyse oder Wirbelschichtverfahren thermisch zersetzt werden. Diese Verfahren entfernen den Kunststoffanteil des Verbundmaterials, sodass Kohlenstofffasern übrig bleiben, die dann mithilfe der Nasspapierherstellung zu verfilzten Fasermatten verarbeitet oder zu gerichteten Fasern umorganisiert werden können.
Die Forscher berechneten, dass Kohlenstofffasern aus Kohlenstofffaser-Verbundstoffabfällen mithilfe eines Wirbelschichtverfahrens gewonnen werden könnten. Dies erfordert nur 5 Dollar pro Kilogramm und weniger als 10 % der Energie, die zur Herstellung der primären Kohlenstofffasern benötigt wird. Im Wirbelschichtverfahren hergestellte recycelte Kohlenstofffasern weisen kaum einen geringeren Elastizitätsmodul auf, und die Zugfestigkeit ist im Vergleich zu primären Kohlenstofffasern um 18 bis 50 % geringer. Dadurch eignen sie sich für Anwendungen, die eher hohe Steifigkeit als Festigkeit erfordern. „Recycelte Kohlenstofffasern könnten für nicht-strukturelle Anwendungen geeignet sein, bei denen ein geringes Gewicht erforderlich ist, wie beispielsweise in der Automobil-, Bau-, Windkraft- und Sportindustrie“, sagte Meng.
13) Neue Technologie zum Recycling von Kohlenstofffasern in den USA entwickelt
Im Juni 2016 tränkten Forscher am Georgia Institute of Technology in den USA Kohlenstofffasern in einem alkoholhaltigen Lösungsmittel, um das Epoxidharz aufzulösen. Die getrennten Fasern und Epoxidharze konnten wiederverwendet werden, wodurch die Kohlenstofffaserrückgewinnung erfolgreich realisiert wurde.
Im Juli 2017 entwickelte die Washington State University außerdem eine Technologie zur Rückgewinnung von Kohlenstofffasern. Dabei wird eine schwache Säure als Katalysator verwendet und flüssiger Ethanol bei relativ niedrigen Temperaturen zur Zersetzung von duroplastischen Materialien eingesetzt. Zersetzte Kohlenstofffasern und Harz werden getrennt aufbewahrt und können einer Reproduktion zugeführt werden.
14) Entwicklung der 3D-Drucktechnologie für Kohlefasertinte im LLNL-Labor, USA
Im März 2017 entwickelte das Lawrence Livemore National Laboratory (LLNL) in den USA die ersten 3D-gedruckten Hochleistungs-Kohlefaserverbundwerkstoffe in Luftfahrtqualität. Mithilfe des 3D-Druckverfahrens Direct Ink Transmission (DIW) entstanden komplexe dreidimensionale Strukturen, die die Verarbeitungsgeschwindigkeit für den Einsatz in der Automobil-, Luft- und Raumfahrt-, Verteidigungs-, Motorrad- und Surfbranche deutlich verbesserten.
15) Die Vereinigten Staaten, Korea und China kooperieren bei der Entwicklung von Kohlefasern für die Stromerzeugung
Im August 2017 arbeiteten der Dallas-Campus der University of Texas, die Hanyang University in Korea, die Nankai University in China und weitere Institutionen gemeinsam an der Entwicklung eines Kohlenstofffasergarnmaterials zur Stromerzeugung. Das Garn wird zunächst in Elektrolytlösungen wie Salzlake getränkt, wodurch sich die Ionen im Elektrolyt an der Oberfläche der Kohlenstoffnanoröhren anlagern und beim Spannen oder Dehnen des Garns in elektrische Energie umgewandelt werden können. Das Material kann überall dort eingesetzt werden, wo es zuverlässig kinetische Energie liefert, und eignet sich zur Stromversorgung von IoT-Sensoren.
16) Neue Fortschritte in der Forschung zu Holzlignin-Kohlefasern, die von Chinesen und Amerikanern gewonnen wurden
Im März 2017 stellte das Spezialfaserteam des Ningbo Institute of Materials Technology and Engineering mithilfe der zweistufigen Modifizierungstechnologie aus Veresterung und radikalischer Copolymerisation ein Lignin-Acrylnitril-Copolymer mit guter Spinnbarkeit und thermischer Stabilität her. Durch das Copolymer- und Nassspinnverfahren wurden hochwertige Endlosfilamente hergestellt, und nach thermischer Stabilisierung und Karbonisierung wurde die kompakte Kohlenstofffaser erhalten.
Im August 2017 mischte das Forschungsteam von Birgitte Ahring an der University of Washington in den USA Lignin und Polyacrylnitril in unterschiedlichen Anteilen und wandelte die gemischten Polymere anschließend mithilfe der Schmelzspinntechnologie in Kohlenstofffasern um. Die Studie ergab, dass der zugesetzte Ligninanteil von 20–30 % die Festigkeit der Kohlenstofffaser nicht beeinträchtigte und voraussichtlich zur Herstellung kostengünstigerer Kohlenstofffasermaterialien für Automobil- oder Flugzeugteile eingesetzt werden könnte.
Ende 2017 veröffentlichte das National Renewable Energy Laboratory (NREL) Forschungsergebnisse zur Herstellung von Acrylnitril aus Pflanzenresten wie Mais- und Weizenstroh. Dabei werden die Pflanzenstoffe zunächst in Zucker zerlegt, anschließend in Säuren umgewandelt und mit kostengünstigen Katalysatoren zu den gewünschten Produkten kombiniert.
17) Japan entwickelt das erste kohlenstofffaserverstärkte thermoplastische Verbundchassis
Im Oktober 2017 entwickelten die japanische Agentur für integrierte Forschung und Entwicklung für neue Energiebranche und das National Composites Research Center der Universität Nagoya erfolgreich das weltweit erste Fahrzeugchassis aus kohlenstofffaserverstärktem thermoplastischem Verbundwerkstoff. Sie verwendeten einen automatischen Direktformprozess für langfaserverstärkte thermoplastische Verbundwerkstoffe, bei dem Kohlenstofffasern und thermoplastische Harzpartikel kontinuierlich gemischt werden, um faserverstärkte Verbundwerkstoffe herzustellen. Anschließend wurde durch Erhitzen und Schmelzen das thermoplastische CFK-Fahrzeugchassis erfolgreich hergestellt.
5. Vorschläge zur Forschung und Entwicklung der Kohlefasertechnologie in China
5.1 Zukunftsorientiertes Layout, zielorientiert, Fokus auf den Durchbruch der dritten Generation der Kohlefasertechnologie
Chinas zweite Generation der Kohlefasertechnologie hat noch keinen umfassenden Durchbruch erzielt. Unser Land sollte eine zukunftsorientierte Strategie verfolgen, indem es seine entsprechenden Forschungseinrichtungen zusammenbringt und sich auf die Erfassung von Schlüsseltechnologien konzentriert. Der Schwerpunkt liegt auf der Forschung und Entwicklung von Technologien zur Herstellung von Hochleistungskohlenstofffasern der dritten Generation (d. h. auf die Technologie hochfester und hochmoduliger Kohlefasern für die Luft- und Raumfahrt anwendbar) und der Entwicklung von Technologien für Kohlefaserverbundwerkstoffe, darunter die Herstellung leichter und kostengünstiger Kohlefasern für große Mengen in den Bereichen Automobil, Bau und Reparatur, additive Fertigungstechnologien für Kohlefaserverbundwerkstoffe, Recyclingtechnologien und Rapid-Prototyping-Technologien.
5.2 Koordinierung der Organisation, Stärkung der Unterstützung, Einrichtung großer technischer Projekte zur kontinuierlichen Unterstützung der gemeinsamen Forschung
Derzeit gibt es in China zahlreiche Institutionen, die sich mit der Forschung im Bereich Kohlefasern befassen. Die Kräfte sind jedoch verstreut, und es fehlt an einer einheitlichen Organisation der Forschung und Entwicklung sowie an einer starken Finanzierung für eine effektive Koordinierung. Ausgehend von den Entwicklungserfahrungen hochentwickelter Länder spielen die Organisation und Gestaltung von Großprojekten eine entscheidende Rolle für die Entwicklung dieses Technologiefelds. Wir sollten uns auf Chinas führende Forschungs- und Entwicklungskräfte konzentrieren, angesichts der bahnbrechenden chinesischen Forschungs- und Entwicklungstechnologie für Kohlefasern Großprojekte starten, die gemeinsame technologische Innovation stärken und das Niveau der chinesischen Kohlefaserforschung kontinuierlich steigern, um den internationalen Wettbewerb im Bereich Kohlefasern und Verbundwerkstoffe zu stärken.
5.3 Verbesserung des Bewertungsmechanismus der Anwendungseffektorientierung technischer Leistungen
Aus der Sicht der ökonometrischen Analyse der SCI-Artikel werden chinesische Kohlenstofffasern als hochfeste Leistungsmaterialien in verschiedenen Forschungsbereichen eingesetzt. Bei der Herstellung und Aufbereitungstechnologie von Kohlenstofffasern liegt der Schwerpunkt jedoch auf Kostensenkung und einer geringeren Forschungsintensität, wodurch die Produktionseffizienz verbessert wird. Der Herstellungsprozess von Kohlenstofffasern ist langwierig, die wichtigsten Technologiepunkte und die Produktionshürden sind hoch. Er erfordert eine multidisziplinäre und technologieübergreifende Integration. Technische Hindernisse müssen überwunden werden, um die Forschung und Entwicklung im Bereich der Kernaufbereitungstechnologien mit niedrigen Kosten und hoher Leistung effektiv voranzutreiben. Einerseits müssen die Investitionen in die Forschung verstärkt werden, andererseits muss die Leistungsbewertung wissenschaftlicher Forschung abgeschwächt und die anwendungsorientierte Bewertung technischer Errungenschaften stärker in den Mittelpunkt gerückt werden. Der Schwerpunkt sollte nicht mehr auf der quantitativen Bewertung der Veröffentlichung von Artikeln, sondern auf der qualitativen Bewertung des Werts der Ergebnisse liegen.
5.4 Stärkung der Ausbildung von Spitzentechnologie-Talenten
Die Hightech-Eigenschaft der Kohlefasertechnologie bestimmt die Bedeutung spezialisierter Talente, und ob sie über hochmodernes technisches Kernpersonal verfügen, bestimmt direkt das Forschungs- und Entwicklungsniveau einer Institution.
Aufgrund der F&E-Verbindungen in der Kohlefasertechnologie sollten wir der Schulung des Verbundpersonals besondere Aufmerksamkeit schenken, um die Koordination und Entwicklung aller Verbindungen sicherzustellen. Darüber hinaus zeigt die Entwicklungsgeschichte der Kohlefaserforschung in China, dass der Zustrom von Technologieexperten oft ein Schlüsselfaktor für das F&E-Niveau einer Forschungseinrichtung ist. Die Aufrechterhaltung der Bindung von Kernexperten und F&E-Teams an Produktionsprozesse, Verbundwerkstoffe und Hauptprodukte ist für eine kontinuierliche Technologieverbesserung wichtig.
Wir sollten die Ausbildung und den Einsatz spezialisierten Hightech-Personals in diesem Bereich weiter intensivieren, die Bewertungs- und Behandlungsrichtlinien für Talente im Bereich Technologieforschung und -entwicklung verbessern, die Ausbildung junger Talente intensivieren, die Zusammenarbeit und den Austausch mit ausländischen Spitzenforschungseinrichtungen aktiv unterstützen und ausländische Spitzentalente energisch einführen usw. Dies wird einen großen Beitrag zur Förderung der Entwicklung der Kohlenstofffaserforschung in China leisten.
Zitat von-
Analyse der Entwicklung der globalen Kohlefasertechnologie und ihrer Bedeutung für China. Tian Yajuan, Zhang Zhiqiang, Tao Cheng, Yang Ming, Ba Jin, Chen Yunwei.Weltweite wissenschaftlich-technische Forschung und Entwicklung.2018
Beitragszeit: 04.12.2018